方磊 何海熙
在工業制造領域,生產成本高、工序復雜、質量管控難、安全事故風險高,是煉鐵行業亟待解決的問題,獲得2024年中國金屬學會冶金科學技術特等獎、2024年度全國第四屆智能制造創新大賽一等獎的南鋼基于多模態感知的三位一體煉鐵解決方案解決了此項難題。
2019年,南鋼攜手中冶賽迪信息和金恒信息科技組建數智化團隊,打造煉鐵智慧集控中心,搭建一體化管控平臺,將新一代信息技術與煉鐵工藝技術和南鋼60余年積累的煉鐵專家經驗深度融合,以多模態智能感知、跨工序協同優化等技術手段,開發了智能應用模型200余套,創造出“成本、質量、安全”三位一體的數智化煉鐵新模式,并于2021年上線應用,取得了顯著成效,實現年創綜合經濟效益5.3億元、鐵水一級品率提升13%、年均減排二氧化碳54.6萬噸、零安全事故。
成本控制:
降本增效的創新實踐
成本是體現企業競爭力的重要因素。南鋼團隊從原料和操作兩個維度入手,深挖降本增效潛力,以保障高爐穩定順行為中心,以“工藝機理分析—性能精準預測—反饋循環優化”為技術主線,研發了一體化配煤配礦和操作協同優化模型集群,有效應對了煉鐵原料(煤炭和鐵礦)物理化學性能復雜多變及市場價格波動帶來的挑戰。
同時,南鋼依托一體化智能管控平臺,圍繞“原燃料質量穩定、高爐爐況順行、鐵水質量穩定、優質高效低耗”四大目標,開發了推焦計劃排程智能優化、煉焦智能加熱、爐溫智能預測、操作爐型識別及優化、爐況智能診斷等智能化應用模型集群,不斷提升高爐操作管理和決策的科學性。該系統應用后,一體化配煤模型降低成本2元/噸鐵,一體化配礦模型降低成本10元/噸鐵,操作協同智能優化模型集群折合鐵水成本降低42元/噸,年均鐵水成本降低54元/噸,并且每年減少CO2排放約54.6萬噸,實現經濟效益與環保效益的雙贏。
此外,南鋼煉鐵智慧中心的建設也推動了生產管理模式的變革。該中心通過優化科室和車間數量、縮減管理層級,將48個車間整合為35個,操作崗位從120個減少到69個,人員優化比例達到41%。同時,在智慧中心的運營中,該中心不斷完善和優化生產流程,加強與供應鏈、物流和環境保護等關鍵環節的協同,實現資源的高效利用和生產流程的優化。
質量提升:
全流程管控的精細化管理
質量是企業生存的根本。南鋼項目團隊搭建“原—焦—球—燒—高”大原料生產管理框架,優化了原料流程的結構與功能,并實現煉鐵全流程物料動態跟蹤和預警,其行業首創的物料跟蹤系統和國內首個料倉多料口在線預測模型,根據入爐成分、時間等信息進行正向預警和反向關聯操作,實現異常原因快速追溯,有效破解了行業共性難題,確保了煉鐵全流程管控的精細化管理,為產品質量提升提供了精準的數據保障。在原料場的改造中,南鋼在行業內首創刮板機自動平料、布料車自動往復布料、焙燒機臺車自動加油、造球智能整粒等大原料工序數智化應用技術,打造出智慧料場、帶式球團“黑燈工廠”產線,實現操作無人化、少人化,現場感知可視化,生產控制一鍵化和運營決策智慧化,為全工序物料精細化管理奠定了堅實基礎。
質量過程管控領域系列智能模型應用后,實現了對生產的智能分析診斷和精準操控,將從原料至高爐的過程產品和鐵水質量顯著提升,包括混勻料SiO2偏差由0.31%降至0.14%,燒結礦R2一級品率由81%提升至98%,FeO穩定率由69%提升至95%,鐵水一級品率由83%提升至96%。
安全保障:
智能監測與管理的全面防線
安全是員工福祉與企業持續繁榮的基石。南鋼團隊融合設備智能監測與運維技術以及大規模遠距離安全集中控制技術,構建了一套涵蓋“操作—運維—管理”的集中管理體系,為煉鐵生產筑起了一道堅固的安全防線。
借助“機器視覺+知識嵌入+視頻聯動”的創新組合,該系統對危險區域和關鍵倉庫等敏感地帶實現視頻彈窗即時報警,為遠程操作人員提供精準輔助決策信息,顯著提升現場安全管理的效能。
通過整合機器視覺、機器人巡檢、光纖聽診、設備診斷等前沿技術,南鋼成功打造出一條具備多模態感知能力的皮帶智能管理示范線。同時,南鋼也搭建了設備智能維護系統,確保關鍵設備的異常狀態能夠被即時捕捉并迅速處理,有效保障了設備的平穩與安全運行。
基于機器視覺、三電綜合安全防護、融合通信等先進技術,南鋼在鐵區全域實施了2300個視頻監測點、144個防入侵監測點、50臺火災和氣體報警主機、1000路視覺協同系統,形成了跨工序、跨系統的大規模、遠距離集控技術體系,對工控網絡通信狀態實施全面統籌管理,極大地提高了消防與安全生產的感知、監測、預警、處置和評估能力,實現了零安全事故。
南鋼通過深度整合多模態感知智能與協同優化技術,實現了11項行業首創技術、20余項行業領先技術的突破,成功構建了“成本、質量、安全”三位一體的數智化煉鐵新模式。這一創新舉措極大地提升了企業的核心競爭力,確保了生產安全,提高了產品品質,并有力地推動了企業的可持續發展。這一實踐不僅為鋼鐵行業推進智能制造提供了寶貴經驗,還在煉鐵行業樹立了新的標桿,引領南鋼煉鐵向行業燈塔地位邁進。
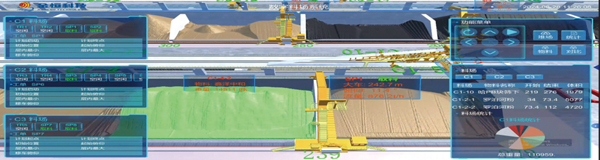
圖為南鋼鐵區智慧料場(南鋼供圖)
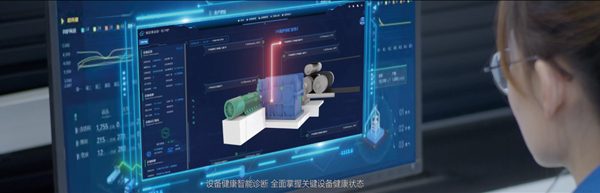
圖為南鋼煉鐵設備智維系統(南鋼供圖)
【新知】
追求技術極致 破解行業難題
張殿華
2024年,鋼鐵行業普遍存在“降本不穩定、穩定不降本”的現象,南鋼卻通過這套數智煉鐵新模式,交上了一份滿分答卷。其背后,是南鋼煉鐵人大規模應用“AI(人工智能)+制造”技術、追求技術極致所帶來的效果。
一是在高復雜度、強耦合工藝條件下獲取配煤配礦的全局最優解,是煉鐵屆一直面臨的共性難題。南鋼煉鐵通過自主研發“跨時域非線性梯度自適應”算法,實現“100多項約束+秒級求解速度+唯一最優解”,破解了行業共性難題。相比原模式,該模型在維持爐況穩定的情況下,降低鐵水成本12元/噸。
二是在行業內首創物料跟蹤技術,實時跟蹤質量變化,有效破解了長流程煉鐵的行業共性難題。同時,南鋼開發了一系列協同優化模型集群,高爐爐溫預報、燒結終點預報、煉焦加熱預報的準確率均超過了90%,助力高爐燃料比降低21千克/噸,每年降本4.2億元。
三是應用了多模態智能感知關鍵技術,打造出智慧料場、“黑燈工廠”,實現了生產遠程化、一鍵化控制,大幅改善工人工作環境,提高生產穩定性。
近年來,南鋼憑借在智能化轉型過程中的優異表現,獲得了行業內外的高度關注,不僅彰顯了其作為行業領軍者的實力與擔當,更為整個鋼鐵行業的數智化升級提供了寶貴經驗和示范引領。
《中國冶金報》(2025年01月14日 04版四版)