中國冶金報社
記者 羅忠河 報道
“中國鋼鐵工業協會成立電爐鋼分會是我們電爐鋼行業的一件幸事,在此提前表示熱烈祝賀!”從事電爐鋼研究40多年的北京科技大學碳中和研究院教授、綠色低碳鋼鐵冶金全國重點實驗室主任朱榮,聽到鋼協即將成立電爐鋼分會的消息,在2月19日接受《中國冶金報》記者采訪時喜悅之情溢于言表。他認為,電爐鋼分會的成立必將對引導和推動我國電爐鋼的健康有序高質量發展起到有力的促進作用。
在采訪中,朱榮高度肯定了鋼協在推動電爐鋼研究和發展方面所做出的努力。比如,鋼協黨委書記、執行會長何文波,副書記兼秘書長姜維等親自帶隊到北科大實驗室,就電爐鋼發展進行調研、交流、探討和指導;朱榮團隊創新提出的近零碳排電弧爐煉鋼工藝,被中國鋼鐵工業協會確定為8項世界前沿重點低碳共性技術之一;等等。
針對《中國冶金報》記者提出的我國電爐鋼技術發展現狀和趨勢話題,朱榮如數家珍、侃侃而談——
我國電爐鋼發展現狀及面臨的問題
談到我國電爐鋼的發展現狀時,朱榮介紹,電爐煉鋼長期經濟效益不如轉爐煉鋼,加上廢鋼資源不足,我國電爐鋼總體而言發展相對緩慢。目前,我國電爐鋼產能約2億噸,實際產量更低。據有關統計,2021年,我國電爐鋼占比為10.7%,達到近10年峰值;2023年回落至9.7%。目前,我國電爐鋼占比在10%左右,遠低于美國70%左右、歐洲50%左右、日本30%左右的電爐鋼占比,與“十四五”規劃的15%占比目標相比也存在一定的差距。
在裝備、技術方面,他說,近年來,我國電爐鋼技術在低碳冶煉、高效生產和智能控制領域均取得顯著突破。在低碳冶煉技術方面,他們團隊推出的“風光儲一體化”供電模式,結合氫能、生物質燃氣作為集速氧槍燃料,探索零碳冶煉路徑,已在河鋼集團張宣科技和中信泰富特鋼靖江基地試點進行工程示范。在高效冶煉技術方面,電爐冶煉周期縮短至30分鐘~35分鐘,噸鋼電耗降至300千瓦時~350千瓦時,電極消耗低于1千克/噸鋼。在智能冶煉技術方面,AI(人工智能)算法與大數據技術廣泛應用,爐況監控機器人、自動取樣系統等設備逐步應用。
不過,他也坦承,總體來講,國產電爐跟國外電爐是有一定差距的,因為國外電爐的技術裝備發展時間長、相對成熟,目前我國電爐裝備還是以進口為主。其實,中冶系國內設計院自主研發的新型電爐設計思路也不錯,需要從國家層面給予大力支持。盡管我國電爐鋼生產技術及裝備整體來講與國外先進電爐相比也有一定的差距,但一些單元技術實現了并跑甚至領跑。比如,電爐底吹技術在國內外率先實現了工程化,供電及氧槍技術成功替代了進口,生產技術指標已達到國際領先水平。
對于我國電爐鋼發展緩慢的原因,朱榮認為有以下幾個方面:
一是廢鋼資源問題。我國是發展中國家,目前整個社會廢鋼蓄積量有限,加上廢鋼回收體系不夠完善,我國廢鋼年回收量也就在2.5億噸左右。另外,轉爐鋼冶煉時也大量添加廢鋼,每噸鋼添加達到200千克左右,甚至更高,與電爐鋼爭奪廢鋼資源。這樣,完全依靠廢鋼冶煉的電爐鋼發展自然受限。
二是生產成本問題。由于電價相對偏高,為了降低成本,我國電爐鋼生產企業一般采用避峰就谷的生產模式,即大多是白天不干、晚上生產。即便如此,我國電爐鋼生產成本也高于轉爐鋼,產能利用率長期在50%左右波動。
三是廢鋼質量問題。據朱榮介紹,上世紀90年代以前,我國電爐鋼曾以生產特鋼為主;之后因房地產市場鋼材需求旺盛轉向生產普鋼,大多生產線材、螺紋鋼,對廢鋼質量要求相對不高;“十四五”以來,房地產市場低迷,加上面臨巨大的碳減壓力,電爐鋼又回歸到部分生產結構鋼和特鋼。這就遇到了廢鋼質量問題。廢鋼成分復雜、雜質多,全廢鋼冶煉高品質鋼材技術難度大,像高品質汽車板的銅含量要求低于0.08%。以前日本的廢鋼曾大量出口到我國,主要是銅含量達到0.3%的廢鋼,有的甚至達到0.6%,廢鋼中銅元素不好去除。“如何利用全廢鋼電爐流程生產高品質鋼,實現廢鋼的高質化利用,這是一項世界性難題,也是我們目前要解決的。”朱榮如此強調。
創新提出近零碳排電弧爐煉鋼工藝
鋼鐵工業碳排放占我國總碳排放量的16%左右,是實現“雙碳”目標的關鍵。傳統電弧爐煉鋼碳排放量盡管只有轉爐鋼的1/3(全廢鋼噸鋼坯二氧化碳排放在600千克左右),但相對碳中和目標仍較高,需進一步降低碳排放。為此,朱榮帶領科研團隊經過近10年的研究,創新提出了近零碳排電弧爐煉鋼工藝。接著,他從能量來源碳近零、冶煉過程碳近零、原料生產碳近零3個方面詳細介紹了如何進行工藝流程創新,實現電爐煉鋼全過程近零碳排放。
在能量來源碳近零方面,利用太陽能、風能等不產生碳排放的綠色能源,將其轉化為電能,如果將這部分綠色電能高效利用于煉鋼過程中,即可從能量來源上達到碳近零的目標。朱榮認為,由風光互補發電系統供能、儲能系統進行調節的電弧爐微電網,可以充分利用風光的互補優勢,在使用清潔能源的同時,可獲得更低的成本,保證電弧爐平穩生產。據測算,風光互補+谷電的平均供電成本為0.2元~0.3元/千瓦時,使得電弧爐生產的能源成本大幅下降,同時實現能量供給碳近零的目標。
在冶煉過程碳近零方面,核心就是非涉碳煉鋼冶煉工藝操作,即在不涉碳條件下,完成煉鋼的冶金任務,包括熔池脫磷、鋼液脫氣、泡沫渣形成、輔助能源提高冶金效果等。目前,氫能燒嘴、生物質氣燒嘴、無碳發泡劑、全廢鋼潔凈化冶煉技術等部分研究成果已經在生產中得到了實踐驗證,取得了較好的冶金效果。比如,氫氧集束射流燃燒無二氧化碳排放,火焰穩定性好,助熔效率高;生物質粉劑、二氧化碳氣體替代傳統碳粉造渣可以減少碳排放,再結合在線能效評價系統,優化全程泡沫渣覆蓋效果;采用二氧化碳噴吹控氮技術,脫氮速率可提升至氬的9.6倍,終點氮含量可降至0.0043%;熔池內采用氧氣—氧化鈣噴吹技術快速降磷,磷含量可降至0.009%,能耗可降低10千瓦時/噸鋼;電能高效利用,中空電極噴吹、電弧長度調節等技術提高熱效率至85%以上。
在原料生產碳近零方面,電弧爐冶煉需要使用各種主輔原料,在冶煉消耗過程中也會間接產生碳排放。要實現近零碳排放,采用非涉碳原料生產技術是降低原料碳排的關鍵之一。目前主要有氫基直接還原煉鐵、輔料生產綠電化、等離子熱風窯爐、降低含碳原料能源消耗等技術。比如,采用氫基直接還原煉鐵技術結合光伏制氫等綠氫生產技術,可以在直接還原鐵生產流程中達到近零排放的目標;采用等離子熱風窯爐+碳捕集技術,煅燒石灰/白云石碳排放減少20%以上;低碳耐火材料:微波干燥、等離子熱風煅燒降低生產能耗,材料碳排放減少35%。
朱榮告訴《中國冶金報》記者,他們團隊采用近零碳排電爐煉鋼新工藝,在新設計的近零碳排5噸中試電弧爐上驗證測算,煉鋼工序最終極限碳排放可降低到64千克/噸鋼。“若2060年中國鋼鐵產量8億噸中80%采用該工藝,碳排放可減少至現有水平的10%以內,為全球鋼鐵業碳中和提供重要的參考路徑。”他強調。
我國電爐鋼技術未來發展方向
對于“十五五”電爐鋼技術的發展方向,朱榮認為重點關注以下幾方面技術:
一是要加強廢鋼快速處理、分選、檢測技術研發。朱榮指出,廢鋼分選與檢測是電爐煉鋼低碳化的基礎。需重點研發AI視覺識別技術,結合激光誘導擊穿光譜(LIBS)實現銅等殘余元素的精準識別與分級。同時,推廣廢鋼預處理技術,如廢鋼破碎、磁性分離及氯源去除工藝,可降低二[惡][口]英生成風險并提升鐵元素收得率。
二是要加強低碳電爐冶煉技術創新與能效提升。朱榮認為,低碳冶煉技術需多路徑突破,比如采用生物質炭粉噴吹技術可降低噸鋼碳排放60千克~70千克,氫基還原技術通過氫氣替代碳作為還原劑,有望實現噸鋼降碳150千克以上。同時,開發二氧化碳底吹強化熔池技術,結合埋入式噴粉實現高效脫磷,可縮短冶煉時間至25分鐘/爐。
三是要推動電爐大型化與智能化升級。朱榮主張,推動大型電爐規模化應用,采用數據孿生煉鋼技術,實時優化溫度、供氧量等參數來提高潔凈化水平。智能化改造需突破三大瓶頸:強化終點控制,采用鋼液連續測溫與光譜分析技術,實現碳含量和溫度的精準預測;加強動態調度,基于AI算法協調電爐與連鑄工序,縮短等待時間5分鐘~8分鐘/爐;推進能效管理,集成電—氧匹配優化系統,通過分階段能效評價降低噸鋼電耗至280千瓦時以下。
四是要實現全廢鋼電爐冶煉高品質鋼技術突破。朱榮介紹,中國工程院院士、北科大教授毛新平承擔的國家自然科學基金重大項目——“變革性低碳鋼鐵制造流程理論與技術”,這是基金委近幾十年支持設立的鋼鐵行業唯一重大項目。其中有兩個子課題,一個是廢鋼高質化利用技術,即在原料端,從基于外形、尺寸等的評級和分析,發展到從化學成分的角度進行分類分級,從而實現廢鋼高質化利用;另一個是潔凈化電爐煉鋼技術,由朱榮團隊承擔,即在冶煉端要盡可能剔除氮、硫、銅等典型有害元素,實現潔凈化冶煉。
五是要強化源網荷儲微電網技術應用。朱榮建議,構建“電爐—儲能—可再生能源”耦合系統,比如通過智能負荷管理,將電爐功率調節納入電網輔助服務,獲取調峰補償收益;強化區域協同,即在廢鋼資源富集區建設微電網,實現廢鋼—電力—熱能的梯級利用,提升綜合能效。
總之,朱榮認為,隨著我國廢鋼蓄積量、產量的增多,采用全廢鋼電爐冶煉技術實現綠色高效低碳智能生產高品質鋼材是我國鋼鐵行業未來轉型發展的必由之路。
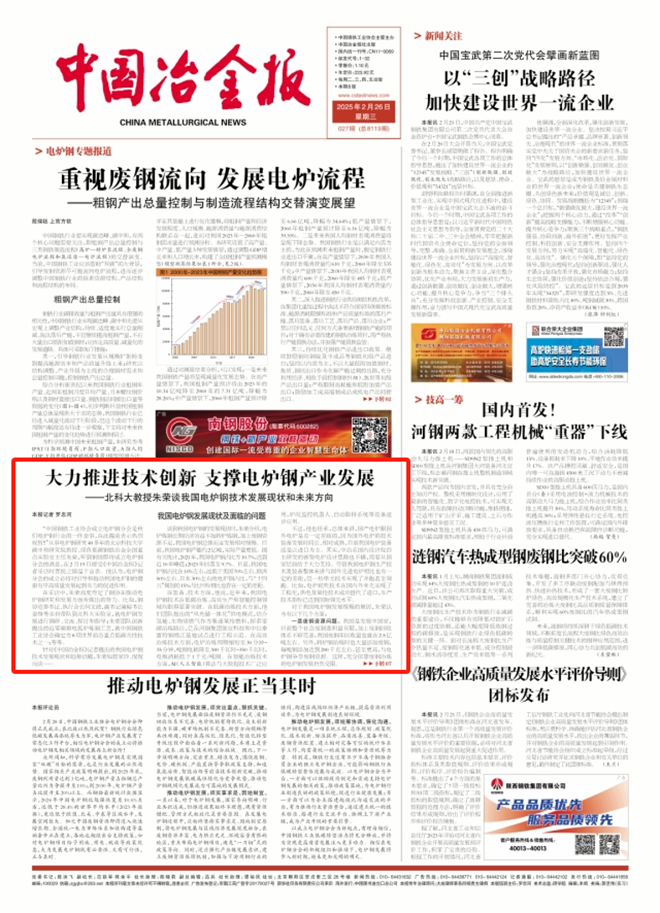