編者按
鋼鐵,現代工業的脊梁,正在經歷一場由科技點亮的綠色嬗變。全球首個氫冶金示范工程投產,全廢鋼電弧爐工藝實現突破,零碳板材工廠開建,低碳排放鋼標準發布……憑借“向科技要綠色”,“碳減法”和“生態加法”與日俱增,天藍地綠水清的美麗中國畫卷徐徐鋪展。憑借“向科技要綠色”,鋼鐵企業“脫胎換骨”,傳統產業“發出了新枝,生出了強枝”。憑借“向科技要綠色”,“綠鋼”碩果加速涌現,沿著產業鏈上下游不斷延伸、拓展,為經濟社會發展帶來無限活力。
我們欣喜地看到,經過多年的科技創新,中國鋼鐵不再滿足于在廠區播撒一抹綠意、為能源轉換發光發熱、做消納社會廢棄物的“城市幫手”,而是尋求更加深刻的變革——DNA(基因)層面的綠色重塑。
因綠而美,因綠而強!科技與生態比翼齊飛,中國鋼鐵“創新本色”與“綠色底色”不斷交融碰撞、蔓延輻射,成為“新質生產力本身就是綠色生產力”的鮮明注腳。今天,我們以筆尖和鏡頭捕捉定格鋼鐵產業低碳技術變革重要瞬間,講述中國鋼鐵“綠色進化”背后的科技故事。
中國冶金報社
記者 米颯 楊立文 通訊員 鐘辰 左蜜琳 王楊 楊媛媛 王帥 報道
春江水暖鴨先知,經濟活力看鋼鐵。
3月初,在全球最大鋼鐵企業——中國寶武旗下的幾大鋼鐵生產基地,各項低碳排放鋼產品生產有條不紊,這些產品將被應用于交通、能源、建筑、電力等行業。
在上海,寶鋼采用全廢鋼電爐冶煉技術路線生產的超低碳排放吉帕鋼在冷軋C008“黑燈工廠”下線,全流程可減碳60%,將用于知名品牌新能源汽車的生產制造。

圖為寶鋼股份冷軋廠“黑燈工廠”。(本報記者 顧學超 攝)
在安徽馬鞍山,馬鋼大軸重重載車輪于去年先后完成減碳超30%的產品發布及供貨。去年底,搭載馬鋼高速車輪的全球最快的高鐵列車CR450動車組已經完成樣車設計并成功下線。眼下,研發團隊正在開展一系列科學試驗和性能驗證,為動車組早日投入商業運營創造條件。
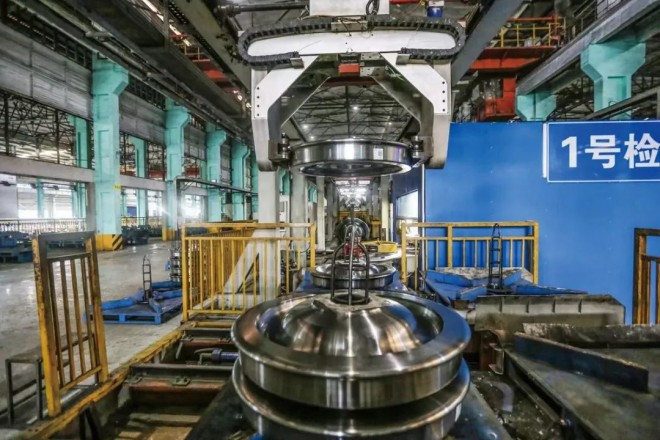
圖為馬鋼全球首款低碳45噸軸重重載車輪。(許然 攝)
在山西太原,太鋼火熱的生產線上,降碳比例達70%的高表面/冷成型用鋼SPHC-LCE熱軋鋼帶正在快速下線準備運往某大型集團,將被加工成最新款的國際知名品牌手機、平板等3C產品的精密零部件。
……
綠水青山就是金山銀山。被認為是最難降碳的行業之一的鋼鐵行業,近年來做好創新這篇大文章,加速向綠色低碳“新賽道”切換,用“綠鋼”支撐起經濟社會發展的全面綠色轉型,激發經濟新活力。
若問有何“奧秘”?看鋼水奔騰,鋼鐵“熔爐”煉出綠色生產力。
“氫”風如貴客,一到便繁華。
今天,革命性的冶金工藝在鋼鐵行業逐步落地。
從氫冶金生產線產出后,氫基直接還原鐵(DRI)與廢鋼一起被投入到近零碳排電弧爐中冶煉,經過精煉、連鑄等工序,變成一塊塊汽車板材料。這是去年12月16日,河鋼全球首條氫冶金綠色汽車板連鑄生產線在河鋼集團張宣科技投產時的場景。在投產現場,張宣科技特鋼公司副總經理呂艷偉被在場的記者們團團圍住,氫基直接還原鐵,裝在他手中玻璃瓶里的黑色小顆粒,吸引了大家的目光。
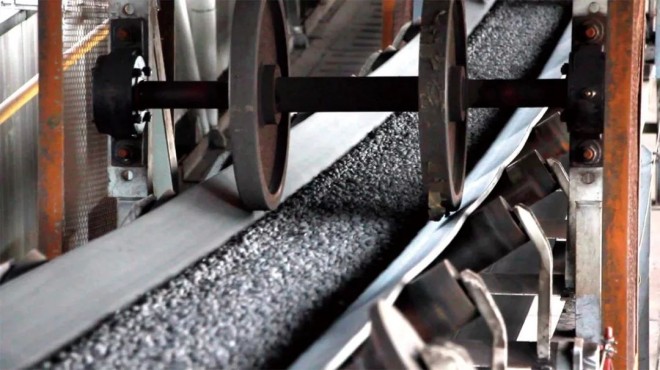
圖為張宣科技氫基直接還原鐵輸送場景。(李廣明 攝)
世界鋼鐵協會的統計數據顯示,與傳統的高爐—轉爐長流程相比,按照不同的金屬收得率折算,以不同的原料(廢鋼/氫基DRI)生產同樣一噸鋼水為基準進行計算,使用氫基直接還原煉鐵替代原有高爐煉鐵,可實現的年降碳量約等于9萬輛汽車一年產生的碳排放總量。
今天,走進位于河北張家口的河鋼集團張宣科技,120米高的氫基豎爐巍然矗立。生產綠色汽車板材料的主要原料氫基直接還原鐵,就“誕生”于這座全球首例120萬噸氫冶金示范工程中。
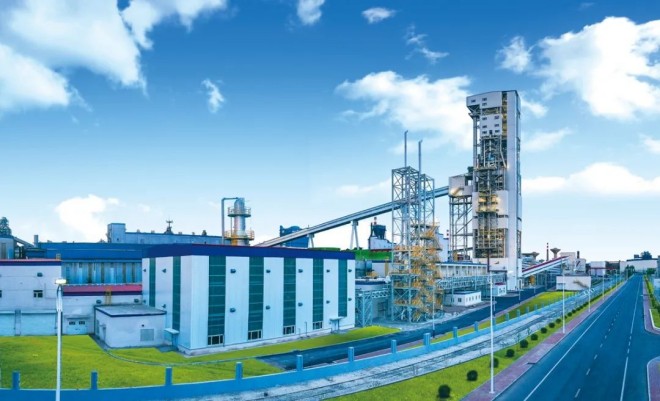
圖為河鋼全球首例120萬噸氫冶金示范工程外景。(河鋼 供圖)
在工廠生產運行時,摸索出最適宜的各項工藝參數控制范圍,明晰這些工藝參數之間的內部關系,實現長周期、低成本的連續穩定生產,是張宣科技在該項目投產后遇到的最主要的挑戰。張宣科技技術中心三級專家覃開偉告訴《中國冶金報》記者,2023年以來,該公司科研人員用2年時間讓一系列技術指標有了明顯突破,形成了獨有的核心技術,包括焦爐煤氣的深度凈化技術、“二氧化碳脫除+二氧化碳精制”的碳捕集再加工利用技術、氫基豎爐高效穩定生產技術、公輔及原料相關的其他核心技術。其中,首次在氫基直接還原工廠中引入整套的CCUS(碳捕集、利用和封存)裝置,可以在原基礎上進一步降低噸DRI產品直接碳排放約15%,并且制成的二氧化碳產品還可出售,產生經濟效益。
經過幾年的運行,氫冶金工序的潛力在張宣科技得到進一步挖掘。
尋求良好的經濟價值和多元產品是張宣科技氫冶金下一步的發展方向。釩、鈦、鎳鐵礦富含多種有價金屬,應用前景廣闊,利用價值巨大,推進釩鈦礦氫還原技術的工業化應用、鎳礦粉在球團和氫冶金配加的工業試驗等,加快形成氫冶金合金化產品序列,將使“氫基豎爐+高效電爐”新型短流程工藝技術優勢得到進一步釋放。
去年,張宣科技氫冶金公司相繼開展鎳礦球及高鈦球工業實驗,使氫冶金非鐵元素產品多樣化,原料更具有經濟性優勢,創造出更大的經濟效益。今年,張宣科技將與河鋼材料院合作實施釩、鈦DRI熔分工業試驗,借助多元化產品“工業生產”挖掘多元素DRI用途,不斷提高DRI產品核心競爭力。
張宣科技技術中心副主任李洋告訴《中國冶金報》記者,自全球首例120萬噸氫冶金示范工程安全順利生產以來,張宣科技共申請氫冶金相關專利69項,獲得授權專利27項,其中發明專利7項;申報氫冶金相關標準11項,其中《煉鋼用氫基豎爐直接還原鐵》《氫基豎爐直接還原用球團》2項行業標準已被工信部批準立項。接下來,他們還將繼續推進氫冶金的創新和發展。
今年春節前,一直忙碌在氫冶金產線的張宣科技氫冶金公司技術質量科科長閆軍帶來了好消息,“鋼鐵煙氣微生物固碳產蛋白試驗研究”項目取得了新進展,在實驗期間通過優化工藝氣的氫氧比、通氣比和氨氮濃度,成功提高了氫氧化菌生物質產率和蛋白含量。這一項目由河鋼集團與澳大利亞必和必拓礦業公司共同發起,由西安交通大學承擔研發試驗。
未來,西安交通大學開發的電能驅動的微生物固碳產菌體蛋白技術若能成功應用于氫冶金二氧化碳煙氣中的高值化轉化,不僅將在利用氫冶金開發高附加值產品,進一步促進非鐵元素多樣化等方面具有重要意義,還將在應對蛋白類糧食安全等方面發揮重要作用。
在廣東湛江,寶鋼股份湛江鋼鐵零碳高等級薄鋼板工廠項目正在抓緊建設。預計今年底,這個具備約180萬噸近零碳板材年產能力的工廠就將投入運營。
打造“近零碳”工廠是中國寶武一次新的嘗試。這一項目不僅在生產流程上確保“潔凈”——將創新應用“氫基豎爐+電爐”進行短流程冶煉,利用廠內現有軋鋼設施生產高等級薄鋼板產品;還積極布局綠電綠氫能源項目,利用南海地區光伏、風能配套“光—電—氫”“風—電—氫”綠色能源,并通過碳捕集、森林碳匯等實現綠氫全流程零碳生產。
未來,有了大量穩定的綠能供應,湛江鋼鐵的綠色變革將更進一步。
去年8月份,湛江鋼鐵國內首套百萬噸級氫基豎爐項目已實現168小時連續滿負荷生產,順利通過周達產功能考核,成功驗證了高氫(70%氫氣含量)冶煉條件,也驗證了該工藝的技術可行性和高水平運行能力。
該項目可同時使用焦爐煤氣、天然氣、氫氣作為原料氣,比例可靈活調整,具備從富氫、高氫至全氫還原的試驗條件,為探索氫冶金技術搭建更廣闊的工業試驗平臺。根據工藝特性,氫基豎爐相對傳統高爐工序減碳至少60%以上,即每年可減少二氧化碳排放50萬噸以上,相當于再造一個500平方公里的森林,而在將來廣泛應用綠氫、綠電后,每噸鋼全流程減碳可達到80%以上。
湛江鋼鐵在積極探索綠色低碳冶金工藝過程中,還形成了“工藝氣體靈活調配”“中低品位球團直接還原及產品應用技術”“冷態直接還原鐵產品處置及應用”等系列自有知識產權的領先技術,進一步豐富了國內氫基豎爐直接還原煉鐵生產應用領域的工業經驗。
廢鋼是一種重要的可再生資源。
坐落在渤海灣中心地帶的河北省唐山市,是鋼鐵生產大市,是國內規模最大、品種最全的型鋼、棒線材、板帶材和焊管等產品生產供應基地,也是國家發展改革委等七部委確定的開展廢舊物資循環利用體系建設重點城市之一。
眼下,唐山的鋼鐵企業正在探索如何高效利用廢鋼資源。
2月27日,位于曹妃甸的首鋼京唐正在為試驗55%比例的大廢鋼比冶煉技術做最后的準備。
轉爐廢鋼比是指在轉爐煉鋼過程中廢鋼的加入量占金屬料裝入量的比例。廢鋼比例越高,降碳效果往往就越顯著。
“轉爐大廢鋼比冶煉的關鍵在于,如何在鐵水熱平衡之外,高效、低碳且低成本地提供廢鋼熔化所需的大量熱量,并實現廢鋼的高效熔化、熱量利用率的提升以及鋼液質量穩定性的保證。”首鋼技術研究院京唐技術中心首席工程師董文亮告訴《中國冶金報》記者,目前,最新試驗的各項方案已經就緒,他對試驗結果很有信心,且已經開始著手推進后續轉爐高效低成本補熱技術和鋼液質量穩定性控制技術的開發,進一步優化和完善轉爐大廢鋼比冶煉技術。
信心來自于實踐。去年10月15日,首鋼京唐順利實現轉爐單工序50%大廢鋼比汽車板IF鋼7爐連澆生產。此舉在長流程工藝低碳煉鋼技術上達到行業領先水平。
常規轉爐煉鋼中使用的廢鋼比一般在10%~20%。為實現更大程度的降碳,首鋼京唐不斷優化工藝、精進冶煉技術,持續提高廢鋼加入比例。但如果廢鋼比達到40%以上,便會對鋼水溫度、鋼水成分等造成諸多不良影響。此后的每一次提升都將是對歷史的突破、對極限的挑戰。
一邊是生產順穩,一邊是低碳創新,如何在保證產品質量的同時,探索更高比例廢鋼的轉爐冶煉技術,持續推進煉鋼工藝降碳減排工作?
熱量平衡、廢鋼熔化、成分控制……這些專業術語落在產線上,就是作業區面對的各種異常和問題。
“我們專門成立了汽車板大廢鋼比冶煉專項攻關組,針對生產過程中出現的異常和問題點,一項一項地分析,逐項攻關。我們借助京唐特有的‘全三脫’(脫磷、脫硫、脫碳)工藝,制訂了‘三步補熱’(在脫磷、脫硫、脫碳時加入補熱劑)法。在此基礎上,我們還不斷優化廢鋼添加配比,來保證廢鋼熔化時機。一系列措施下來,這些問題迎刃而解。”首鋼京唐煉鋼部煉鋼作業區日班作業長丁立豐那段時間一直緊盯汽車板大廢鋼比冶煉專項攻關,他告訴《中國冶金報》記者,生產過程中,他們作業區還把這些操作環節固化下來,形成了操作規章制度。
“對轉爐單工序大廢鋼比冶煉而言,當廢鋼比超過40%后,各項技術難度都呈指數級增加,哪怕是1%的提升,都需要整個攻關團隊100%的全力托舉。”參與攻關的制造部低碳管理室低碳工程師王章嶺回憶道,為了實現50%廢鋼比常態化生產,他們組織多次轉爐大廢鋼比試驗,整個團隊群策群力,實現了多個低碳汽車板新產品的大廢鋼比批量生產,用最快的速度、最短的時間、最經濟的成本,探索出了一條具有京唐特色優勢的低碳技術路徑。
50%大廢鋼比低碳鋼冶煉穩定后,首鋼京唐建立了轉爐煉鋼大廢鋼比特色降碳工藝路線,先后成功實現了轉爐單工序50%以上大廢鋼比低碳鋼7爐連澆生產和50%以上大廢鋼比汽車側圍外板生產,產品覆蓋汽車板(含外板)、鍍錫板、家電板、酸洗板、熱軋板等。
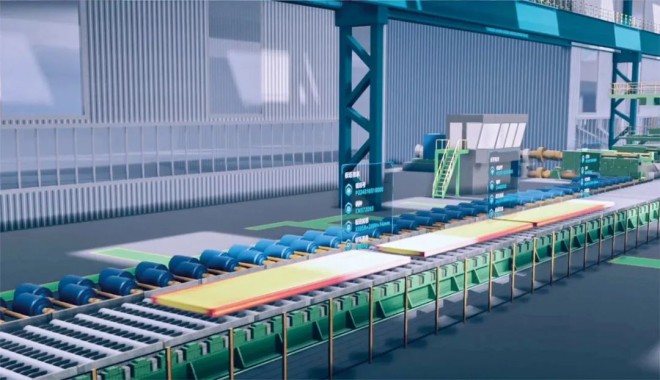
圖為首鋼京唐中厚板4300產線軋鋼數字孿生系統。(首鋼京唐 供圖)
在唐山樂亭,唐鋼的技術人員對大廢鋼比冶煉技術的研究同樣如火如荼。在實施高廢鋼比的情況下,鋼水終點命中率如何保證?他們通過分析研究廢鋼特性和冶煉工藝,在保持熱平衡的基礎上,合理確定轉爐廢鋼用量和加入時機。在冶煉過程中,廢鋼難熔化的技術壁壘怎么破?團隊創新設計高廢鋼比專用氧槍噴頭,并優化轉爐供氧制度,使轉爐吹煉時間延長、轉爐底吹強度提高、熔池攪拌時間增加,一舉解決難題,從而順利實現高廢鋼比長流程工藝生產。多加廢鋼導致熔池溫度驟降問題如何解?他們利用優化廢鋼結構、設計最佳易熔廢鋼比等手段,有效改善熔池溫度和成渣條件,保住了溫度,也保住了質量,還讓鋼鐵材料更“綠色”。一系列方案實施后,唐鋼依托長流程冶煉工藝路徑生產的品種鋼添加廢鋼比例突破54.7%,達到國內領先水平。據介紹,目前唐鋼大部分家電用鋼綠色產品已經鎖定了可實現穩定生產的高廢鋼比長流程冶煉工藝路徑。
從沿海到內陸,對廢鋼高效利用的探索仍在繼續。
在湖南婁底,漣鋼采用超高比例回收料生產工藝冶煉的首卷冷軋熱成型鋼于2月17日成功下線,鋼材含廢鋼占比高達60%,較常規工藝產品的二氧化碳排放減少43%。
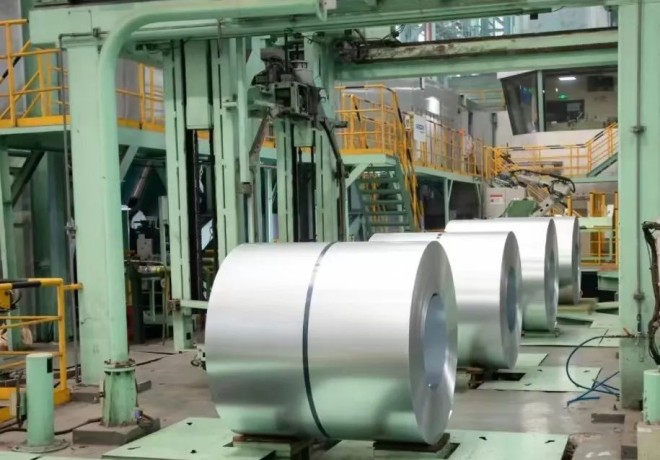
圖為漣鋼冷軋熱成型鋼生產現場。(孫遠平 攝)
此前,同樣為了破解高廢鋼比冶煉難題,漣鋼開展的“基于大廢鋼比的綠色高效冶煉與質量控制關鍵技術”項目,不僅需要開發一系列新的制造技術,還為相關基礎研究的深入開展提供了“漣鋼平臺”,吸引了眾多高校的關注,一場場科研攻關隨即在漣鋼產線和高校間并進——
針對熱量不足的問題,漣鋼全盤統籌高爐、鐵水罐、轉爐和LF(爐外精煉爐)等多個工序,開發最優廢鋼配加模型;首創煤氧多層疊加鐵包廢鋼烘烤技術,再配合研發的多LF協同升溫等技術,實現了全工序聯動的高效快速熱補償。
為了加快大廢鋼比冶煉節奏,漣鋼與武漢科技大學聯合開發超高音速新型氧槍噴頭,結合自行研發的大廢鋼比護爐、高效脫磷等技術,實現210噸轉爐供氧強度提升23%、作業率提升13%、平均冶煉周期縮短8分鐘,居行業領先水平。
針對鋼水過氧化嚴重、成分波動大等質量問題,漣鋼開發鐵水預處理脫氮、轉爐高效控氮、LF智能化供電、RH(真空循環脫氣爐)高效脫硫等技術,并與東北大學、北京科技大學聯合開發大廢鋼比夾雜物及殘余元素控制等技術,同時結合北京科技大學毛新平院士團隊開展的大廢鋼比下殘余元素影響及控制研究,突破了大廢鋼冶煉高品質鋼質量控制的諸多技術瓶頸,全系列鋼種的殘余元素滿足質量要求,汽車面板用鋼廢鋼比提升11%,鍍鋅汽車高強鋼廢鋼比提升12%,熱成型鋼廢鋼比提升18%,取向硅鋼廢鋼比提升15%。
……
去年12月30日,中國金屬學會在北京組織召開了由漣鋼等單位聯合完成的“基于大廢鋼比的綠色高效冶煉與質量控制關鍵技術”項目科技成果評價會。評價委員會認為,該項目成果總體達到國際先進水平,其中200噸以上轉爐高廢鋼比條件下高供氧強度冶煉技術生產高品質鋼達到國際領先水平。截至目前,該項目獲授權專利24項,其中發明專利21項;發表論文23篇,SCI(科學引文索引)收錄7篇,形成工藝規范9項。
攻堅于科研、生產一線,歷經9年,漣鋼通過基礎研究、制造技術開發,形成了具有自主知識產權的大廢鋼比綠色高效冶煉技術體系并實現了規模化應用,滿足自身全系列包括超低碳鋼、硅鋼等在內的高端品種的綠色、高效、高質生產需求,相比常規冶煉流程,用于替代鐵礦石的廢鋼用量達745.87萬噸,減少二氧化碳排放1296.54萬噸,總減碳量相當于86.6萬輛汽車1年行駛15000公里的碳排放量。
提升短流程電爐煉鋼比重,是推動鋼鐵業綠色低碳發展的一項重要舉措。根據世界鋼鐵協會去年11月發布的《可持續發展指標報告2024年版》,2023年全球每噸粗鋼生產產生的二氧化碳排放噸數(下稱二氧化碳排放強度)為1.92噸(該指標代表了高爐—轉爐流程產量、以廢鋼為原料的電爐流程產量和以直接還原鐵為原料的電爐流程產量之間的加權平均值)。其中,高爐—轉爐流程的二氧化碳排放強度達2.32噸,而以直接還原鐵為原料的電爐流程和以廢鋼為原料的電爐流程的二氧化碳排放強度分別為1.43噸和0.70噸。
去年5月份,國家發展改革委等五部門出臺《鋼鐵行業節能降碳專項行動計劃》,提出積極發展新型電爐裝備,在符合節能降碳、環保、產業等政策條件下,加快推動有條件的高爐—轉爐長流程煉鋼轉型為電爐短流程煉鋼,到2025年底,廢鋼利用量達到3億噸,電爐鋼產量占粗鋼總產量比例力爭提升至15%。
今年2月8日,工信部對《鋼鐵行業規范條件(2015年修訂)》進行了修訂,形成的《鋼鐵行業規范條件(2025年版)》也指出,鼓勵企業關停退出燒結機、焦爐、高爐等傳統設備,轉型發展低碳煉鐵、電爐煉鋼。
數據顯示,2023年,我國鋼鐵行業廢鋼消耗量約為2.14億噸。但是,受制于廢鋼質量等問題,高爐—轉爐長流程廢鋼消耗量約占70%,電爐短流程廢鋼消耗量僅占約30%。
廢鋼成分復雜、雜質多,如何利用全廢鋼電爐流程生產高品質鋼,實現廢鋼的高質化利用,是一項世界性難題。
不過,在開展廢舊物資循環利用體系建設的重點城市——太原,太鋼正在全力破解這一難題——具有太鋼特色的全廢鋼+電弧爐流程極致低碳工藝開發正在穩步推進。
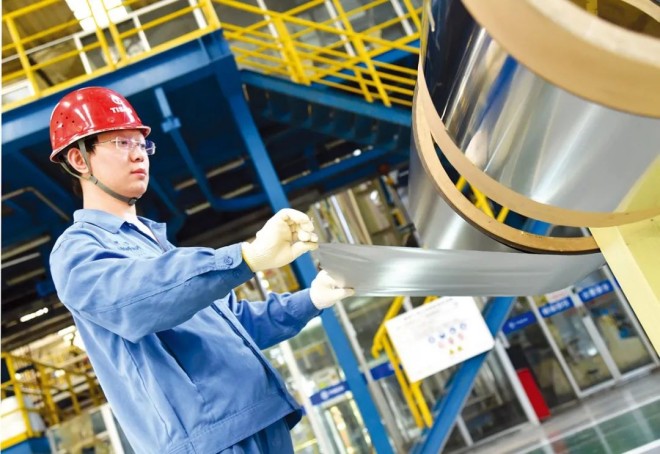
圖為太鋼“手撕鋼”——不銹鋼精密箔材。(特約通訊員 王旭宏 攝)
其高表面/冷成型用鋼SPHC-LCE熱軋鋼帶,依托太鋼160噸高效電弧爐,采用低碳排放優質廢鋼,克服了雜質元素對產品力學性能和鋼質純凈度的影響,滿足了下游客戶對產品≥92%廢鋼回收比的需求,實現了噸鋼碳排放達到0.5噸以下,產品碳足跡較常規高爐+轉爐流程降低70%以上。該工藝于2023年12月份相繼取得ROHS(由歐盟立法制定的一項強制性標準,主要用于規范電子電氣產品的材料及工藝標準)認證、REACH(歐盟對進入其市場的所有化學品進行預防性管理的法規)認證和SCS認證(回收成分認證),認證廢鋼比≥95%。此后不到1年,采用該工藝生產的熱軋卷又成為滿足新出臺的《低碳排放鋼評價方法》標準的首批8個中國低碳排放鋼大類產品之一。
技術進步,標準先行。
2024年10月18日,由中國鋼鐵工業協會組織編制的《低碳排放鋼評價方法》標準正式發布并實施。這一標準的出臺,凝聚了鋼鐵行業內44家企業和機構、逾百位專家的智慧與心血,依托于國內約3.5億噸粗鋼產能排放的大規模數據支持,成為了迄今為止全球同類標準中數據最為詳盡、信息最為豐富的范本之一。該標準的發布和實施,為鋼鐵企業發布綠色品牌、低碳排放產品以及下游用戶開展綠色采購提供了一套科學且系統的依據,能夠助力鋼鐵及上下游全產業鏈、全價值鏈低碳轉型發展。
這一標準發布5天后,在上海舉行的2024年全球低碳冶金創新論壇上,中國寶武首發低碳品牌BeyondECO及系列產品:寶鋼股份冷軋汽車板高強鋼、冷軋汽車板高表面外板,高牌號極低鐵損取向硅鋼、高效高牌號無取向硅鋼,無縫鋼管氣瓶鋼,熱軋建筑用鋼;馬鋼大軸重重載車輪;太鋼高表面冷成型用鋼。這些產品全部滿足新標準。
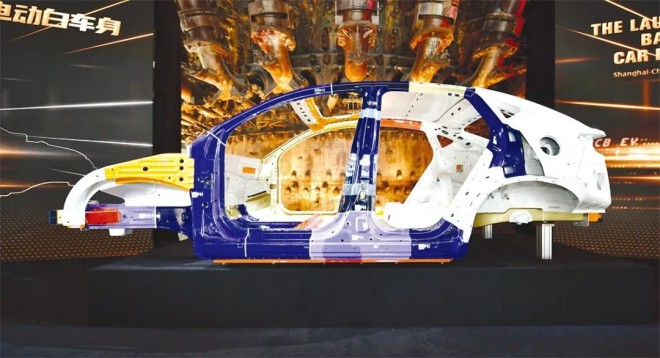
圖為寶鋼股份超輕型、高安全、純電動白車身。(張勇 攝)
在此之前,能否吃透標準,并在產品開發時確保生產組織管理有序協調、低碳資源應用高效、技術投入及成本管控精準,都是橫在企業面前的“攔路虎”。與此同時,隨著市場對低碳產品的需求增加,碳排放正在成為影響國際貿易的新變量。
在此背景下,寶鋼股份積極投身于低碳產品的研發與生產。寶鋼股份各基地精心策劃開展低碳產品的生產驗證工作,建立起了穩定可靠的供應體系。其低碳產品品類豐富多樣,涵蓋熱軋板、線材、普冷板、熱鍍鋅板、電鍍鋅板、取向和高牌號無取向硅鋼、鍍錫板等,并覆蓋了多個應用領域。憑借卓越的產品品質,寶鋼股份已成功為眾多國內外用戶提供優質的低碳排放產品,獲得了市場的高度認可。
去年,寶鋼股份在低碳產品研發領域取得了重大突破。多個基地積極開展多路徑低碳排放產品試制,成功完成碳足跡第三方認證。
在汽車用鋼領域,寶鋼股份構建起領先且完備的整車低碳解決方案能力。通過與多家海內外汽車用戶緊密合作,寶鋼股份推出中國首件全廢鋼全綠電生產的吉帕鋼零件和低碳寶特賽電鍍鋅零件,以及全球首件全廢鋼全綠電生產的第三代超高強吉帕鋼零件,為推動汽車行業綠色低碳發展注入強大動力。
在硅鋼產品領域,去年,寶山基地和青山基地相繼發布低碳排放硅鋼產品。值得一提的是,寶鋼股份的低碳取向硅鋼產品已在全國首臺高電壓等級的大型電力變壓器中成功應用。
鞍鋼亦早早就“嗅”到了“碳”機遇。
2021年,鞍鋼的國外產品客戶陸續要求其提供產品生命周期評價(LCA)報告或碳足跡,并提出未來采購低碳排放鋼的需求和準入條件。彼時,鞍鋼在此方面并未開展過深入研究。鞍鋼股份技術中心環境與資源研究所低碳技術團隊抓住時機,通過開展鞍鋼集團級科研項目,熟悉鞍鋼股份全生產工序的資源、能源消耗以及排放等情況,開展大量的數據收集、清洗、分配與LCA計算工作,完成鞍鋼股份主要產品的生命周期評價,并建立符合鞍鋼生產實際的LCA方法與體系,建成了具有計算、分析、預測等功能的“鞍山鋼鐵碳排放及產品LCA平臺”。《低碳排放鋼評價方法》標準正式發布后,鞍鋼低碳技術團隊第一時間組織技術人員,迅速開展基于標準的熱軋產品碳績效的核算工作,使鞍鋼股份熱軋卷成為中國低碳排放鋼首批發布產品之一。
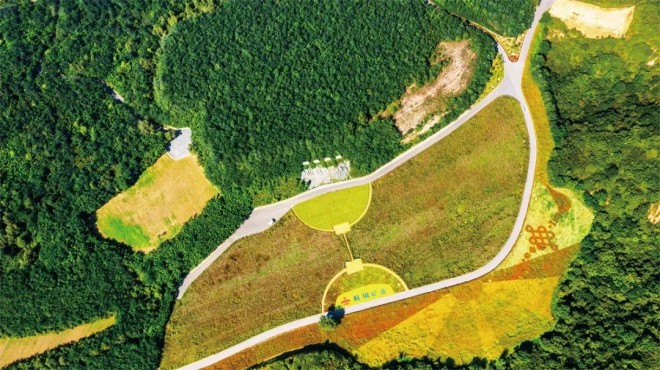
圖為鞍鋼礦山生態園。(鞍鋼 供圖)
隨著越來越多的下游用戶提出低碳排放產品采購要求,國際鋼鐵同行也在積極推廣低碳排放產品品牌。然而,全球范圍內低碳排放鋼標準呈現碎片化和多元化特征,尚未形成統一或互認的標準體系。據統計,全球有幾十個機構或企業在研究低碳排放鋼標準,包括第三方倡議組織、鋼鐵企業、金融機構和下游用戶等。這種標準的不一致性給鋼鐵行業及企業帶來了諸多困擾。如今,符合中國發展特征及資源能源稟賦的《低碳排放鋼評價方法》孕育出更多的降碳可能,秉持著“遵循國際規則、堅持‘共同但有區別的責任’原則”,中國鋼鐵人正積極推進這一標準的國際間互認,力爭為全球鋼鐵減排貢獻中國標準力量。
今天,以標準為炬,綠色鋼鐵之光將照亮更多下游領域,加速更多行業實現綠色變革——
新型馬氏體耐熱鋼,使全球首個第四代煤風電超超臨界機組成為現實,機組效率由第三代的45.4%提升至50.16%,若我國全部采用第四代發電技術,將年均多節煤2億噸。
更高效環保變壓器用極低鐵損取向硅鋼新產品,進一步降低了輸電損耗。在北京冬奧速滑館和雄安新區建設中,搭載寶鋼股份耐熱刻痕取向硅鋼的“超一級”能效立體卷鐵芯變壓器憑借其卓越的性能,實現了30%以上的節電效果。若此類變壓器全面替代我國配電網現有的變壓器,每年減少的碳排放量有望達到1.3億噸,將對我國配電網的節能減排工作產生深遠影響。
電鍍鋅低碳鋼、第三代超高強汽車板、耐微生物腐蝕管材、建筑用耐火耐候鋼、免涂裝鐵塔用耐候鋼……一大批以高強度、耐候、長壽命、可循環為特征的“中國領先”“中國首發”乃至“全球首發”的綠色鋼鐵產品相繼問世,被作為“工業食糧”源源不斷地輸送至千行百業,為國民經濟發展夯基壘臺。
“鋼鐵產業是我們國家的重要基礎產業,實體經濟是國民經濟的根基所在。要繼續努力,把短板補上,把結構調優,繼續為中國式現代化多作貢獻。”習近平總書記的一席話言近旨遠。
草木蔓發,春山可望。隨著綠色生產力結下“綠鋼”碩果,相信在不久的未來,會有更多從“綠起來”到“美起來”“富起來”的鋼鐵故事在神州大地涌現,共同繪就出美麗中國新畫卷。
●2021年2月
中國鋼鐵工業協會提出“抓基礎、謀突破、樹標桿、搭平臺、建標準、創機制、重自律、嚴監管”的24字行業低碳工作指導方針,并發布《鋼鐵擔當,開啟低碳新征程——推進鋼鐵行業低碳行動倡議書》。
●2021年4月22日
鋼鐵行業低碳工作推進委員會在滬成立。
●2022年5月19日
中國首個工業品EPD(環境產品聲明)平臺——中國鋼鐵全產業鏈EPD平臺正式上線。
●2022年8月15日
《鋼鐵行業碳中和愿景和低碳技術路線圖》正式發布,提出碳中和4個階段性目標和系統能效提升、流程優化創新、冶煉工藝突破等6條技術路線。
●2022年12月9日
中國鋼鐵工業協會啟動了全行業極致能效工程,截至2024年底,12家企業已進行極致能效標桿示范公示,全行業能效提升顯著。
●2022年12月
中國鋼鐵工業協會提出“世界前沿低碳共性技術開發支持計劃”,梳理富氫或全氫氣基直接還原技術、近零碳排電爐流程技術等重點突破的八大前沿低碳共性技術方向。
●2024年7月8日
中國鋼鐵工業低碳技術路線圖更新,發布鋼鐵低碳服務平臺。
●2024年10月18日
《低碳排放鋼評價方法》團體標準在滬正式發布。
●2024年10月23日
中國鋼鐵行業首批8個低碳排放鋼大類產品發布。
●2024年11月29日
中國鋼鐵工業協會、世界鋼鐵協會和城市土地學會共同倡議,國內外7家鋼鐵企業、13家世界知名房地產企業、6家院所和協會共同啟動了房地產低碳排放鋼合作倡議,承諾自愿推廣使用低碳排放鋼。
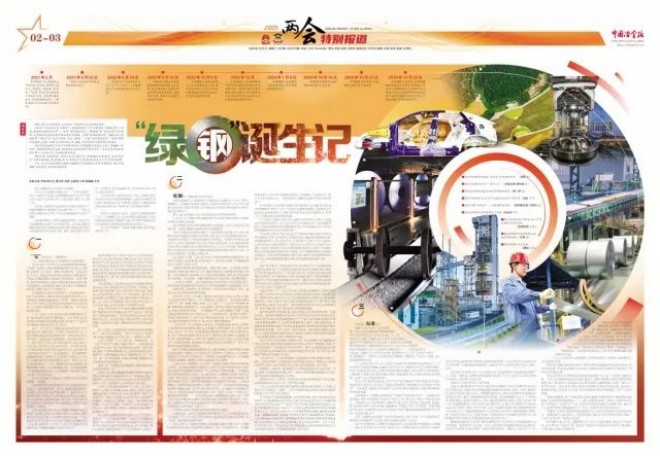